PVDC resin is often used as composite material or monomer material and co-extruded film sheet, and is the most used high-barrier packaging material, among which PVDC coating film is used in a particularly large amount. The PVDC coating film uses polypropylene (OPP), polyethylene terephthalate (PET), etc. as the base material. Due to the high softening temperature of pure PVDC, close to its decomposition temperature, and poor compatibility with general plasticizers, it is difficult to heat and form and it is difficult to directly apply. Most of the PVDC films actually used are copolymers of vinylidene chloride (VDC) and vinyl chloride (VC), and films with particularly good barrier properties made from copolymerization with methyl acrylate (HA).
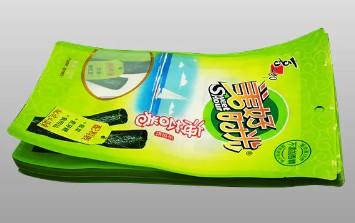
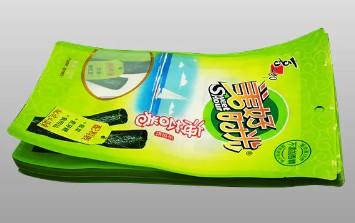
A series of package pouches and film rolls Used for packaging food
PVDC (polyvinylidene chloride) is characterized by low permeability, barrier properties and chemical resistance. my country's PVDC is accompanied by the introduction and development of ham sausage processing technology.
In 2002, the domestic output of PVDC was about 20,000 tons, and it has been widely used in food, cigarette, beverage preservation and taste separation, as well as moisture-proof packaging in chemical, pharmaceutical, electronic and military industries.
The single-layer PVDC film is produced by biaxial stretching blow molding, which has shrinkage, barrier properties and water resistance, and does not decompose under the condition of microwave heating. It is widely used in household plastic wrap; PVDC and polyethylene (PE), polypropylene ( Multi-layer extrusion of synthetic resins such as PP) and polystyrene (HIPS) is used for the packaging of vacuum dairy products and jams. ) composite sheet is suitable for the packaging of easily moisture-absorbing and volatile medicines. Many domestic research institutes and manufacturers focus on the research of PVDC and other resin composite lamination film technology and the high temperature resistance technology of composite film.
PVDC is used in a variety of substrates such as PE, PP, PVC, polyamide (PA), polyethylene terephthalate (PET), etc. Taking biaxially oriented polypropylene film as an example, the oxygen permeability after coating It can be reduced by 1000 times, and the water permeability is reduced by 3 times; the coating can be single-layer or multi-layer, and generally a single-layer coating of 2.5μm can have a good barrier effect.